Biochemical Engineering and BioProcessing Laboratory
The Biochemical Engineering and BioProcessing Laboratory led by Chemical and Biological Engineering Professor and NovaCell Director William J. Kelly, PhD, develops and optimizes scalable bioprocesses, both upstream (i.e., bioreactors) and downstream, for the production of biopharmaceuticals. The lab's current focus is on immuno-oncology products such as CART.
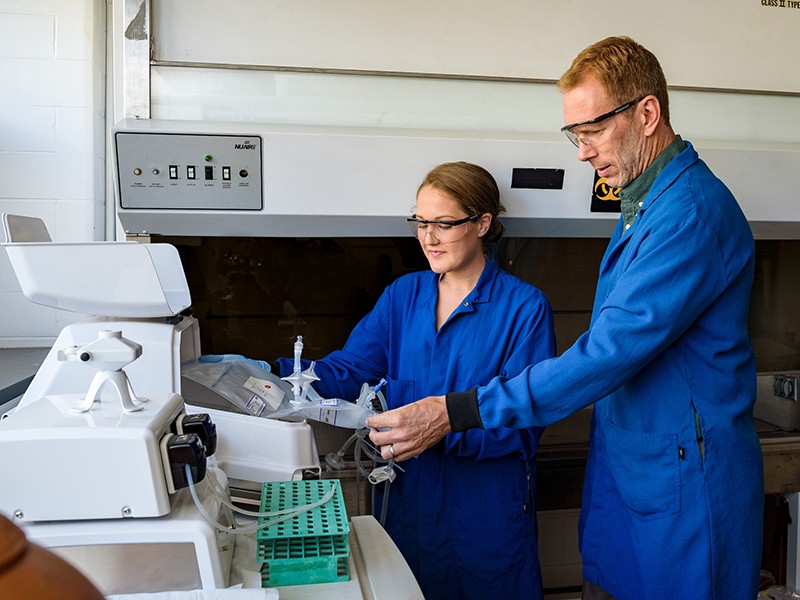
OUR RESEARCH
In CAR-T cell treatments, the patient’s blood cells are extracted, and the T-cells are isolated. These T-cells are exposed to a viral vector that integrates the coding sequence for a chimeric antigen receptor (CAR) that is specific for the kind of cells being targeted by the therapy. In 2017, two products gained FDA approval, including Novartis’s Kymriah and Gilead’s Yescarta to respectively treat B-cell acute lymphoblastic leukemia and B-cell non-Hodgkin lymphoma. An estimated 10-20% of CAR-T batches fail however due to slow growth rates of T cells during the ex-vivo expansion step of the CAR-T process.
For CART processing, clinical-scale T cell activation and expansion is typically done in reactors that are mixed (GE’s WAVE and Miltenyi’s Prodigy) and/or sparged with gas (Wilson Wolf’s G-rex). For micro-scale growth on a 96 well plate, which can be used as a scaled-down bioreactor for T cells, it is difficult to mix and sparge gas and so it is typically not done. The cell growth media generally include the addition of IL-2 anti-CD3 and anti-CD28 antibodies. With that, T cell expansion is usually conducted using beads conjugated to anti-CD3 and anti-CD28 antibodies, which induce a physiological response by binding to T cells to promote growth and proliferation.
Dr. Kelly's group is working on developing a properly scaled down “bioreactor” to improve processing of cell therapy products such as CART therapies. Preliminary work has shown the capabilities of nano-sized magnetic posts for providing mixing and improved oxygen transfer to T cells growing on 96 well plates, and how this can positively impact T cell growth at that microscale. In recent years, more and more pharmaceutical companies are moving toward semi-continuous and perfusion mode operations because they can produce higher cell concentrations more economically. Perfusion processes provide a constant environment for cells through continuous by-product removal and nutrient addition, while retaining the cells in the bioreactor. Dr. Kelly's lab is also focusing on developing more continuous CART processing, including perfusion-based bioreactors.

GRANTS
Title: A Transcriptome-based Model for Improved CAR-T Therapy
Sponsor: National Institute for Innovation in Manufacturing Biopharmaceuticals (subaward of NIH grant, 04/01/2019-03/31/21, NCE Microplate Bioreactor for High Throughput Biopharmaceutical Process Development)
Dates: 03/01/2019 – 09/01/2020
Investigators: Dr. William Kelly (PI) with Dr. Zuyi “Jacky” Huang (co-PI) and Redbud Labs, Inc.
Description: Cell growth rate is a limiting factor in CAR-T therapy research. This grant will support the optimum configuration of Redbud’s bioreactor technology, testing T cells under a variety of conditions and different mediums, and developing a mathematical model that can predict cell growth rate based on conditions.
LAB FACILITIES
- WAVE Bioreactor (1 liter)
- YSI cell culture metabolite analyzer
- Two CO2 incubators
- Two 20l stainless steel steam-in-place New Brunswick Bioreactors