Research
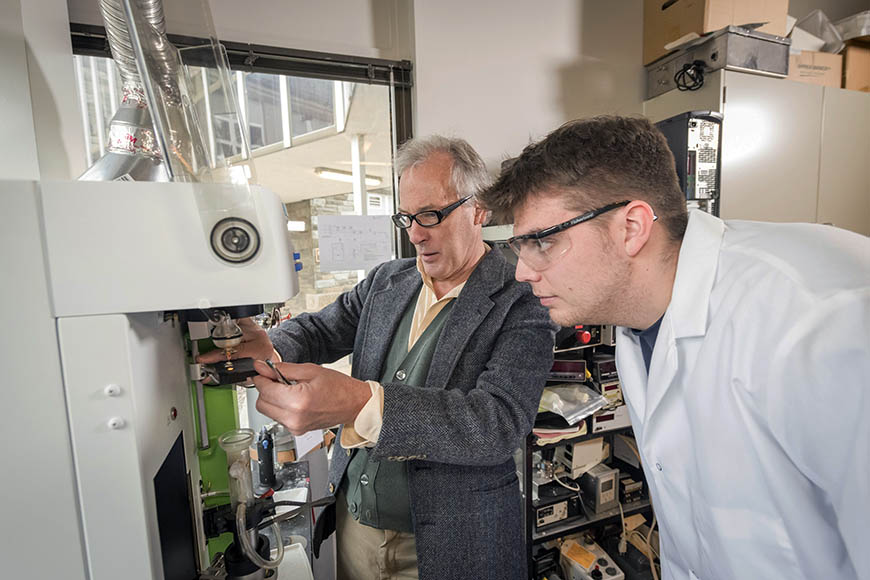
High-temperature CO2 capture agent for improved hydrogen production
Replacing liquid fuels with sustainable alternatives is a particularly daunting challenge. Synthetic liquid fuels—from, for example, the Fischer-Tropsch process, or fuels derived from biomass—all require hydrogen during manufacturing. The bulk of hydrogen today is manufactured by steam-methane reforming (SMR); however, the thermodynamics of this overall process requires it be done in two separate unit operations: a high temperature SMR step, following by a low-temperature water-gas shift (WGS) step.
Our goal in this project is to simplify the process by developing a high temperature CO2 capture agent that would effectively combine the two unit operations. The CO2 sorbent of choice is lithium orthosilicate, Li4SiO4, (LOS); however, the material has very slow kinetics because a product shell of lithium carbonate forms a diffusion limiting barrier around the unreacted core. Our solution to this problem is to create a LOS-like material with a network of pores such that virtually all of the LOS is associated with the surface of the material. We use various synthesis methods to create these nanostructured materials, characterize them using nitrogen adsorption, XRD and evaluate the CO2 sorption kinetics using thermogravimetric analysis (TGA). This project is a collaboration with Professor Chuck Coe.
Understanding and improving lewis acidity in catalysts
Approximately 95% of all man-made products require a catalyst at some point in their manufacture; as such, developing improved catalysts is vital to creating a vibrant, sustainable economy. A typical catalyst consists of a catalytically active species on the surface of an inert, porous substrate (typically alumina or silica). However, it is known that the type of support has a marked effect on catalyst performance: Pt on alumina behaves differently that Pt on carbon, for example. In an earlier study published in the Journal of Catalysis, we showed how differences in surface roughness of a silica support had an effect on vanadia—catalyzed partial oxidation of methanol and propane. A broad hypothesis is that our earlier findings are not unique to vanadia, but also apply to acid catalysts. If so, this creates opportunities to tune the acid strength in subtle, yet important ways. In this effort we will synthesize SBA-15, functionalize the support with acidic materials such as zirconia, titania or stronger organic acids, and vary the supports in a systematic way by adjusting the synthesis conditions. We characterize the catalysts by adsorption, FTIR spectroscopy, and then use them it a suitable test reaction such as alcohol dehydration.
Mesoporous silica as a drug delivery vehicle
SBA-15 is a mesoporous silica originally synthesized at UC Santa Barbara, the diameter of the pores can be tailored between 5 and 10 nm, and the pore surface can be modified to create different functionality. This makes SBA-15 an intriguing candidate as a delivery vehicle for large therapeutic molecules. By altering the surface chemistry of the silica, we can tune the strength of interactions between surface and a drug molecule, thus altering its release kinetics for controlled drug delivery.